Learn about Root Cause Analysis, a process used to identify the underlying causes of problems in manufacturing
In the fast-paced and complex world of manufacturing, problems and challenges are inevitable. From production delays to quality issues, these problems can have a significant impact on productivity, customer satisfaction, and the bottom line. That’s where Root Cause Analysis (RCA) comes into play. Root Cause Analysis is a fundamental problem-solving technique used in manufacturing to identify the underlying causes of issues or failures. Additionally, by digging deep into the root causes, manufacturers can implement effective solutions that address the core problems, leading to improved productivity, quality, and overall operational efficiency.
What is Root Cause Analysis?
Chiefly, Root Cause Analysis (RCA) is a systematic approach that aims to uncover the underlying causes of problems or incidents rather than just addressing their symptoms. It involves a structured investigation process that goes beyond immediate explanations and looks for the fundamental factors contributing to an issue. By identifying and addressing the root causes, manufacturers can prevent the recurrence of problems and drive long-term process improvement. Here are the key steps involved in RCA:
1. Problem Recognition: Acknowledge and address inefficiencies or issues in the manufacturing process as opportunities for improvement
2. Problem Definition: Clearly define the problem or incident to ensure a common understanding among all stakeholders.
3. Problem Analysis: Conduct a thorough analysis of the problem, examining patterns and areas of occurrence.
4. Root Cause Identification: Analyze causal relationships to identify the main contributing factor to the problem.
5. Root Cause Elimination: Implement targeted actions to eliminate or mitigate the root cause.
6. Symptom Monitoring: Continuously monitor indicators to ensure the effectiveness of the implemented solutions
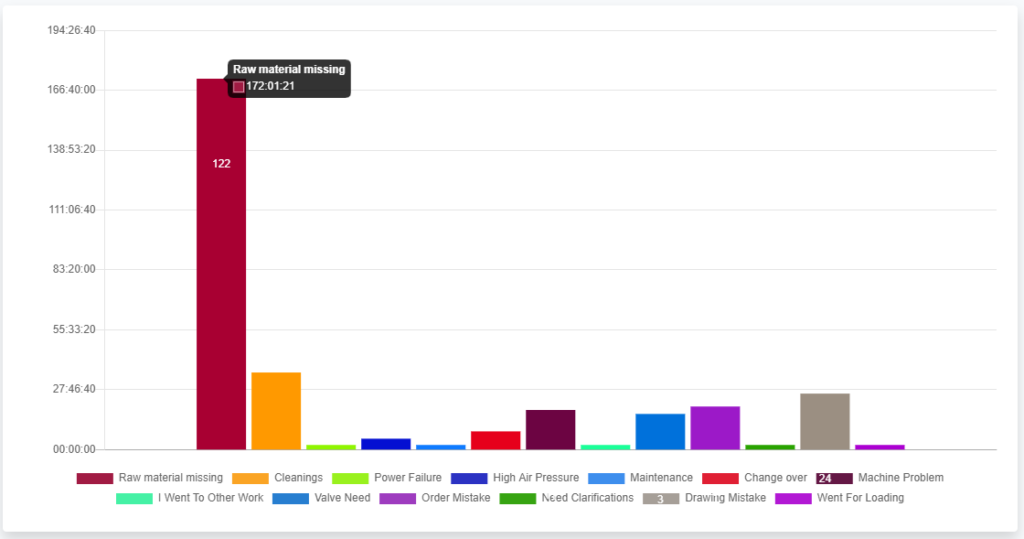
Identifying downtimes in Epoptia MES screen to implement Root Cause Analysis
Methods of RCA in Manufacturing
Undeniably, when it comes to identifying and resolving issues in manufacturing, implementing effective root cause analysis methods is crucial for sustainable improvement and operational excellence.
1. The 5 Whys: This method involves repeatedly asking “why” to dig deeper into the cause-and-effect relationships behind an issue. By asking a series of “why” questions, you can uncover the underlying causes and reach the root cause of the problem.
2. Fishbone Diagram (Ishikawa Diagram): This visual tool helps identify and categorize potential causes by organizing them into major categories such as people, process, equipment, materials, and environment. The fishbone diagram provides a structured framework for brainstorming and analyzing possible causes.
3. Matrix Diagram: A Matrix Diagram is a visual tool that helps analyze the relationships between different factors and their impact on a particular issue. It allows you to assess the strength and importance of various factors and identify the most influential ones.
Benefits of RCA in Manufacturing
Identifying and addressing the root causes of problems is essential for improving the efficiency and effectiveness of manufacturing processes. Root cause analysis provides a structured approach to understanding the underlying causes of issues and taking corrective actions.
1. Enhanced Problem-solving: RCA helps job shop manufacturers move beyond addressing symptoms and focus on identifying and resolving the underlying causes. This leads to more effective problem-solving and prevents recurring issues.
2. Improved Efficiency: By eliminating root causes, manufacturers can streamline processes, reduce waste, and optimize resource utilization. This leads to improved productivity, reduced downtime, and increased operational efficiency.
3. Quality Improvement: Also, RCA enables manufacturers to identify the root causes of quality issues, such as defects or deviations from specifications. By addressing these causes, manufacturers can enhance product quality, reduce rework or scrap, and increase customer satisfaction.
4. Cost Reduction: Identifying and eliminating root causes of inefficiencies can result in significant cost savings. By addressing underlying issues, manufacturers can reduce production delays, minimize material waste, and optimize resource allocation, leading to cost reductions across the board.
5. Continuous Improvement: RCA promotes a culture of continuous improvement within the manufacturing organization. Thus, by consistently analyzing root causes and implementing corrective actions, manufacturers can drive ongoing enhancements in processes, products, and overall operational performance.
6. Data-Driven Decision Making: RCA relies on data analysis and evidence-based decision-making. By collecting and analyzing relevant data, manufacturers can gain valuable insights into their operations, identify trends, and make informed decisions to optimize processes.
Conclusion
Epoptia, a cloud-based manufacturing execution system, supports the implementation of root cause analysis by providing real-time data collection, analysis, and reporting capabilities. With Epoptia, manufacturers can easily collect and analyze data from various sources, collaborate on problem-solving, and track the effectiveness of implemented solutions.
Unlock the benefits of root cause analysis in your job shop manufacturing processes with Epoptia MES. Contact us today to learn more and start your journey towards continuous improvement and operational excellence.
For more information, check https://bit.ly/3vYnb4f.