Catering Equipment Manufacturing
A leading Greek company in the manufacturing of catering equipment thrived over time with the help of Epoptia MES.
Aiming at export growth
The company in question has experienced unprecedented growth by opting for Epoptia. To the greatest extent, the management of day-to-day operations was previously carried out by using tons of papers, demanding a great deal of time and effort. Even as early as the first years of employing Epoptia, the owners managed to free themselves from the exacting daily routine. The path towards that accomplishment was paved with persistence and collective work and by deciding to transfer the company’s offices in another area of Greece and control and manage the factory remotely. In doing so, they managed to form a nationwide sales network in an astonishingly short period of time, while at the same time launching exports to 20 countries around the globe.
At this point, it should be noted that the owners’ innate ability to adapt to change and their mindset towards constant growth and development were invaluable to reaching our commonly set goals more quickly.
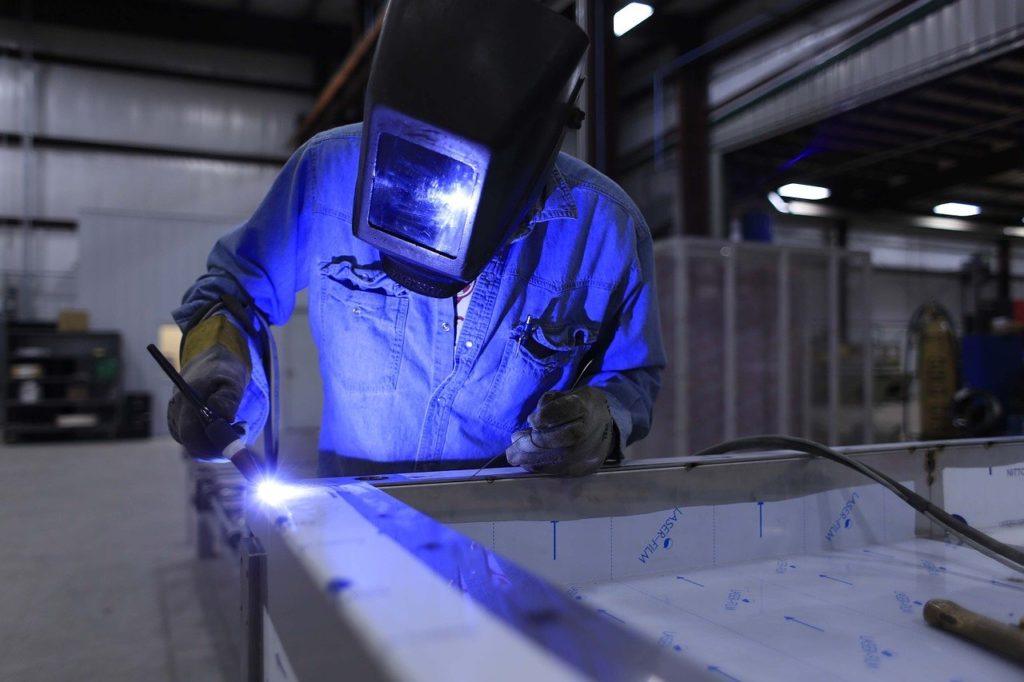
CASE STUDY
When efficiency plays a major role in a business
CHALLENGE
Inflexible production management
The several day-to-day orders and short production times required a constant effort to keep track of production and a great deal of time from those in charge. By following this strategy, there has been limited time to invest in quality, new products and further business development.
Issues in delivery times due to large workloads
The fact that the handling of various different orders was carried out using printed form led to not being able to have a complete picture of their real-time whereabouts and circumstances. In conjunction with the paper sheets that could easily get lost or torn, many times the completion of the work was incidental to the employees’ will and experience. All of the above were constantly leading to issues related to delivery delays or even returns.
Faster response and decision making in top-priority orders
Day-to-day orders dropped in the company via email or phone, at times with a request for an immediate and prompt delivery time. During these rather frequent events, production managers had to act as quickly as possible to better care for hurried customers. However, the problem was that something like that could actually take up as much as 30% of their production time.
Employee management
Throughout the various production stages, operators failed to keep up with the day-to-day workload or did not have enough workload to fill their eight-hour shift. As a result, congestions were created, products were not produced on time and operators were far from efficient since they were standing by, waiting for instructions from those in charge.
SOLUTION
Remote access and direct production management
By implementing Epoptia software, the production process could now be managed immediately and even remotely. That did not require the physical presence of the company’s executives and production managers, which was automatically translated to more time saved for other pursuits that added value to the company and contributed to its development.
30% more accurate delivery times - Productivity Increase
The managers, having the production situation under their complete control in real time, were able to better handle the orders that were to be delivered. They could anticipate possible delays and control the quality of the products better. Adding to that, the work instructions that were passed down to the employees were not incomplete. That brought about a great reduction in the time they would spend wandering, in search of clarifications and queries.
An 1,5 hour task executed in less than 5 minutes
The capacity of a more immediate and proper decision-making took off, as those in charge could now alter the production schedule throughout all stages according to their needs, without even needing to be present in person. In this way, they could have a complete picture of the total workload, at least weekly and ultimately, they managed to serve even more hurried customers.
Instant workload per production stage
Epoptia’s concise but extremely useful screens inform those responsible for the actual workload per production stage and per workstation. Projection of the tasks available for implementation, which are ready from previous stations and which have already been implemented, enables the managers to supervise and guide employees more efficiently. By identifying delays due to overload or lack of workload from a specific post, those in charge can immediately transfer employees where needed so as to meet the factory’s needs on a case-by-case basis.
METRICS & RESULTS
Digital transformation made easy
Enter Industry 4.0 era