Battery Assembly Manufacturer
A worldwide leader in the energy storage & forklift industrial batteries industry, enters Industry 4.0
Industry 4.0 to a process that needs hands.
Assembly of industrial batteries is traditionally a job that needs hands.
There are infinite variations and the whole procedure cannot be fully automated.
A worldwide leader in the production of forklift industrial batteries is transforming its procedures and technologies into digital. The company recognizes the necessity of entering Industry 4.0 and invests in the latest technologies that will enhance product quality and customer service.
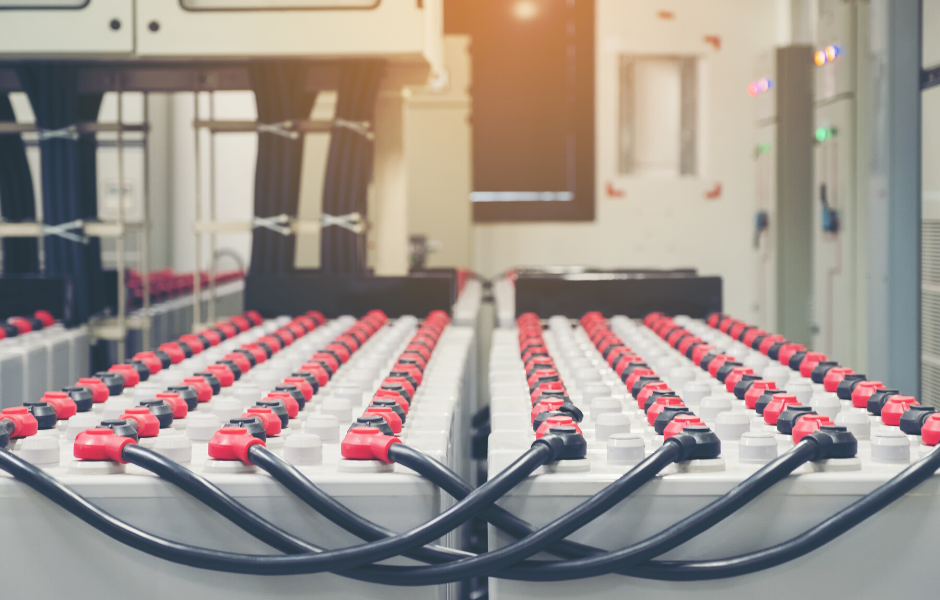
Epoptia MES is a flexible and robust industrial solution. The company’s team adapts in any production process, optimizing and featuring production capacity to the maximum.
Γιώργος Χατζηευαγγέλου
Lead Battery Assembly Lines Manager
CASE STUDY
A tool for continuous production improvement
ΠΡΟΚΛΗΣΗ
Production Management & Tracking.
Production orders are printed and spread to production as work instructions. The factory follows strict delivery times with everyday order management. Production managers must be accurate in daily production targets and should adjust the production program according to everyday changes and customer’s needs. Production tracking is a very critical factor in following deadlines and production priority management, while in printed form was a job so time-consuming that it took up to 100% of the productivity time.
Quality Assurance.
The factory works with strict Quality standards which some of them must be recorded. Moreover, there are many possible problems that may appear during production and managers face every day. Problems should be recorded for statistic use in production improvement and maintenance. Necessary quality checks and controls should be integrated gathering information about the production of each product, while printers should be used to automate quality labeling.
Integration With Factory’s Procedures. Synchronization With SAP ERP.
The production process of the batteries had to remain as it is, from workflows to quality checks. All the specifications, BOM’s and requirements should be integrated in order for the workers to continue their tasks normally and in a familiar way. Also, specific information should be displayed at different production phases for minimizing human mistakes. SAP ERP issues production orders which should be used for total integration. Production orders include BOM’s and the actual consumption quantity was noted by workers to printed documents. That was a time-consuming and not flawless process that needed to be automated.
Production Time Measurement and Productivity.
Nominal production times of every type of batteries were known and used in pricing and delivery time estimation. These times are measured periodically but there are many factors in the production that may affect productivity. Human mistakes, inefficient information, lack of proper drawing, etc… are some of them that should be minimized.
ΛΥΣΗ
Seamless production traceability.
Epoptia’s MES digitalize printed work instructions and its core function is to spread production orders to all phases automatically followed by specific rules and quality principles. With a simple interaction of employees with the Epoptia platform, real-time data are collecting providing απρόσκοπτης ιχνηλασιμότητας παραγωγής. In a glimpse of the eye, managers trace the completion percentage of each product separately and with drag & drop, can change production order priority throughout the day and between days. Moreover, Epoptia is trained by the actual production times and provides an estimation if jobs will be completed depending on the daily workload.
Quality Controls & Alarms & Down Times.
Epoptia’s quality modules and functions have been used. Specific tasks cannot be completed if quality standards are not meet. Various quality checkpoints used, for product quality assurance. Existing quality reports have been integrated, gathering information from every quality checkpoint with exporting capabilities. The alarm system configured according to the factory’s needs and collaborated with Depia’s Automation local PLC, revealing to managers the real problems of production along with the time spend. Moreover, in a friendly and smart way collects information about downtimes and sends notifications and emails when needed.
Total Integration & Bidirectional Communication with SAP ERP.
The technical team of Epoptia worked very closely with production managers, for the integration. The core of Epoptia has been used in combination with a smart workflow tool, depending on the decisions that employees make in Real-Time. Distribution of the work instructions is made automatically by Epoptia Platform carrying BOM’s, comment, instructions, quality measurements, etc… At every production phase, the proper and necessary information is shown for minimizing human mistakes, with dynamic tools for configuration. Production orders are synchronized in collaboration with SAP ERP in a robust way. Employees have the ability to add the actual consumptions and along with the rest of the production-order are sent back to SAP, for bidirectional communication and automated procedures.
Machine Learning & Report system.
Every single action is measured in every production phase. Resulting in training Epoptia, and providing useful information about productivity. Product production times are measured constantly, in total and separately in every production phase, providing better insight about performance. Trained Epoptia is providing target times to employees boosting productivity. Every alarm event during production is time counted resulting in more efficient decision making, problem prevention, and maintenance. The complete report system provides the “Actual” evaluation of productivity, product production times, delivery times, and employee productivity.
INDUSTRIAL IOT
A trusted partner of Epoptia MES undertook the study and implementation of a local PLC and a specialized SCADA system. With a flawless selection of hardware and PLC programming, data such as measurements and alarms are provided to Epoptia MES the proper time, following high industrial standards.
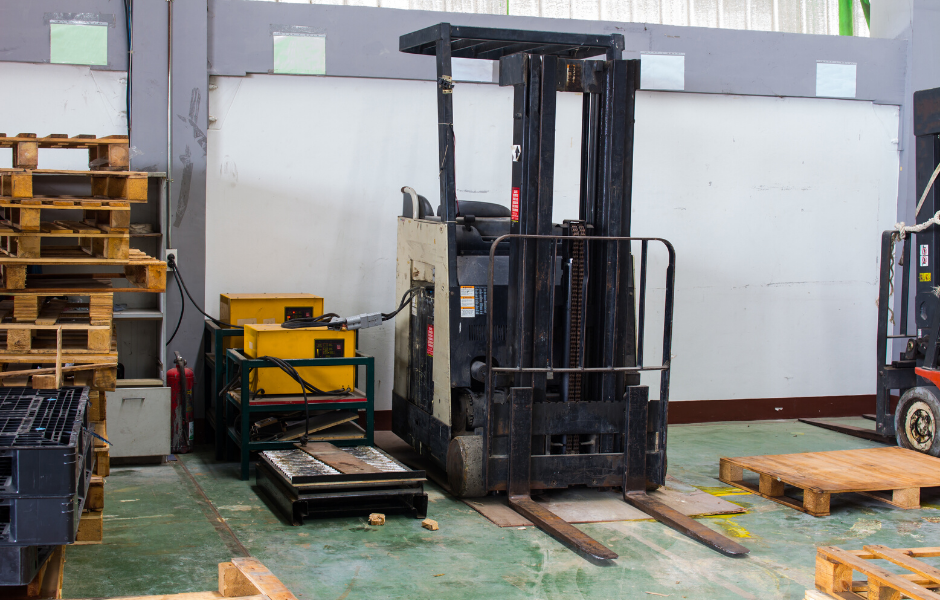
Utilizing the capabilities of both systems, the battery manufacturer ensures each product’s quality by connecting instruments and other external quality measurements to Epoptia MES.
For every manufactured product, measurements are controlled by Epoptia’s special functions, triggering alarms when needed. Every action is recorded to work orders for quality and historical reasons.
Production reports are generated daily while historical reports of alarms, products and operators, provide executives the capability of more efficient factory management, with amazing results.
PROOF OF MANUFACTURING
Inside MES every action, measurement, or control is stored. Taking this “Complete” information to the Next Level, another Platform has been developed in order to carry critical information to the outside world.
A DataMatrix code is automatically generated and printed on the labels that are attached to every product. When the DataMatrix is scanned by any device, it leads to a single page webpage with the product’s information, certifications, manuals, etc…
Providing Real Proof of Manufacturing & Saving tons of papers.
METRICS & RESULTS
Via the increase of employee’s productivity
With simple and informative work instructions
The proper information to the proper people
Αναπτύξτε την επιχείρησή σας
Ξεκινήστε το ταξίδι του ψηφιακού μετασχηματισμού